What is Powder Metallurgy Process?
Powder Metallurgy Process is a type of Metallurgy Process that involves combining tiny powdered particle and compressing them into a specific shape or form and finally heats the compressed metal powders slightly below their melting points in a controlled environment to join the metal particles. The study of powder metallurgy and its technology can be called as Powder Metallurgy Science. It is an old, one-of-a-kind way of producing forms and patterns from ferrous and non-ferrous metals. Powder metallurgy is often used to make household goods and tools for thousands of years.
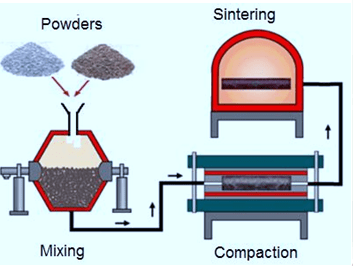
The powder metallurgy method has become the fundamental technique for the manufacturing of bushings, bearings, gears, and a variety of structural elements as technical breakthroughs have been developed and implemented.
Also Read
- Nano Technology – Its Branches and Applications – And More
- Smart Manufacturing Industry 4.0 – Its Applications, Advantages – And More
Powder Metallurgy Process Steps
To convert a powder into a final product, it requires number of steps or process. So, the powder metallurgy consists four fundamental processes, they are
- Powder Preparation
- Powder Mixing and blending
- Compacting
- Sintering
Let us read about these powder metallurgy process steps in detail
Step 1 – Powder Preparation
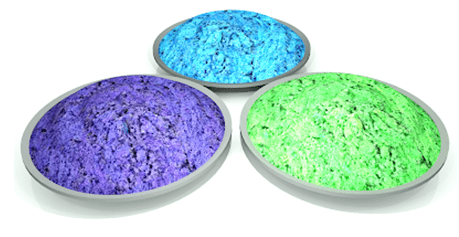
The step 1 in powder metallurgy process steps involves powder preparation. The overall features of powder metallurgy products are determined by the qualities and properties of the powder. Melt Atomization is one of the procedures used to create the powder. In this process, the liquid metal is broken down into small droplets, which cools and solidify into minute particles. Though atomization is the most prevalent technique of creating powder, other methods such as
- Chemical Reduction
- Electrolytic Deposition
- Grinding, And
- Thermal Breakdowns are also used.
All metals and alloys may be turned into powder regardless of the procedure utilized. Prior to combining and blending the powder, its suitability for the powder metallurgy process is reviewed and tested. In the testing and reviewing, they concentrate on
- Powder Flow Rate
- Density
- Compressibility
- Strength
Step 2 – Powder Mixing and Blending
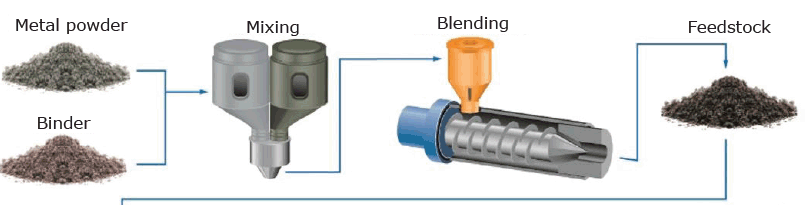
After step 1, the Powder Particles are mixed with additional powders, binders, and lubricants during the mixing and blending process to ensure the finished item has the required properties. Depending on the kind of powder metallurgy process and the needs of the item, blending and mixing can be accomplished wet or dry.
The four most frequent blending and mixing components or parts involve
- Rotating Drum
- Rotating Double Cone
- Screw Mixer On The Interior Of A Drum, and
- Blade Mixer On The Interior Of A Drum
Step 3 – Compacting
Compacting is step 3 in the powder metallurgy process steps, which involve squeezing and compressing the dry powder into a specified shape or mold. When it is done correctly, compacting decreases possible voids and considerably boosts product density. The squeezed and pressurized shape is known as green compact, which indicates that the portion was created through compacting.
- The compacting pressure ranges from 80 to 1600 MPa. Depending on its characteristics, each form of metal powder needs a particular amount of compacting pressure.
- The pressure in soft powder compacting ranges between 100 and 350 MPa.
- The pressure for more robust and harder metals, such as steel and iron ranges between 400 and 700 MPa.
Step 4 – Sintering
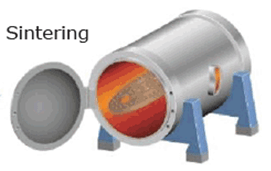
The Step 4 is Sintering. Despite being stretched and squeezed under severe pressure, the green compact is not sturdy enough to be utilized. The green compact is sintered or heated at high temperatures to form a permanent link between the metal particles. The particles of the green compact are pressed together to create a shape during compacting. Sintering, in essence, creates the final useable product or part.
- Sintering is a heat treatment process that involves in the powder metallurgy process in which a large number of compressed pieces are exposed to temperatures high enough to generate enough pressure to enable the loose particles to join and link, producing a solid piece.
- The needed temperature varies depending on the type of metal, although it is always somewhat lower than the melting point of the metal.
- Irrespective of the compacting pressure used, the green compact has minute porous gaps. The material is compressed and pushed under high temperatures during sintering to close the porous areas and reinforce the component.
So, these are the four powder metallurgy process steps that is involved in processing a component.
Also Read
- Thermoplastic Polymer – Its Process, Working, Advantages, Applications and More
- Thermosetting Polymer – Its Process, Working, Advantages, Applications and More
Types of Powder Metallurgy Process
To process a material from raw material to the required final product using this powder metallurgy, there are different types of powder metallurgy processes and they are
1. Conventional Powder Metallurgy Process
2. Injection Molding Process
3. Isostatic Pressing
4. Metal Additive Process
1. Conventional Powder Metallurgy Process
Conventional powder metallurgy process contains all the procedures that involved in the basic powder metallurgy, which includes
- Mixing
- Compacting and
- Sintering of the powder and alloy.
This type of powder metallurgy process is similar to the traditional powder metallurgy procedure, but with the added benefit of contemporary technology.
2. Injection Molding Process
The other type of powder metallurgy process is Injection Molding Process. The capacity to make complicated forms in huge quantities is a distinct advantage of Injection Molding.
- Injection molding powders are particularly manufactured with a binder, such as wax or a thermoplastic. The combination is known as feedstock, which is injected into the mold cavity of a standard injection molding machine.
- When the green compact is removed from the mold, the binder is extracted using heat or solvent processing. During sintering, any leftover binder disappears.
- The injection molding powder metallurgy method is extremely similar to plastic injection molding and high pressure die casting that producing the same delicate and complex geometries.
- The amount of secondary finishing required with powder metallurgy injection molding is the challenge.
The main advantage of Injection Molding Process is the capacity to manufacture good dimensional tolerances in an infinite number of forms with unique geometric characteristics.
3. Isostatic Pressing
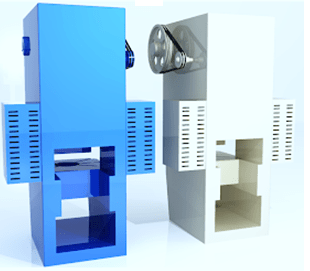
- Isostatic pressing is a procedure that applies the constant or same amount of pressure to the whole surface of the workpiece.
- Every angle, curve, line, and depth of the component has the same density and microstructure when pressure is applied uniformly from all directions. Depending on the requirements of the object being created, isostatic pressing can be done cold or hot.
- When pressing dies are not a possible way to be manufactured due to its particularly massive and complicated, then cold Isostatic Pressing is used.
- Isostatic processing may be performed on a wide range of materials. The needed pressure ranges from a little under 5000 psi to 100,000 psi.
- The powder is molded in wet or dry elastomeric molds. High heat and Isostatic Pressure are combined in hot isostatic pressing.
- The combination of the two elements
- Reduces Porosity
- Increases Density
- Improves Mechanical Qualities and
- Makes Completed Components Usable
- Micro shrinkage is reduced via hot Isostatic powder metallurgy.
4. Metal Additive Process
- The Metal Additive process is a significant advancement in manufacturing techniques and the next way for making the goods we want.
- It is a method that has been used for years to create prototypes for proposed components and sometimes referred to as three-dimensional printing or 3-D Printing. Additive manufacturing creates parts layer by layer from a digital model.
- Metal additive Manufacturing or Metal Additive Process incorporates various technical developments, very efficient, and produces no waste.
- It starts with a powder bed 20 to 100 micrometers thick.
- To melt away the different layers, one or more lasers are applied to the bed. The melting process is repeated layer by layer until the component is entirely created.
Also Read
- What is Thermocouple – Its Types, Working, Advantages, Applications and More
- What is Engine Cam – Its Types, Applications, Advantages, and More
Advantages of the Powder Metallurgy Process
There are vast advantages of Powder Metallurgy Processes, they are
- Eco-Friendliness
- Flexibility
- Neat Net Shape
- Raw Materials
- Repeatability
- Chemical Homogeneity
- Wear Resistance
- Magnetism
Eco-Friendliness:
The powder metallurgy technique is a low-impact manufacturing approach. An incredible 97 percent of the material utilized to manufacture parts using powder metallurgy is included into the finished product. Powder metallurgy generates extremely little waste and produces no scrap. Every particle of powder that enters the process is incorporated into the final component. In addition to being ecologically friendly, reducing waste saves money.
Flexibility
Powder metallurgy, unlike other procedures, can blend and combine several metals and non-metals into a product. With the application of a binding substance, unusual and one-of-a-kind combinations can be combined to form a single part. Complicated metallurgical techniques can be avoided since powder metallurgy can simply blend and condense diverse materials into a single form.
Powder metallurgy can create any form, from complicated and elaborate shapes to basic gears. The continued advancement of its technology is allowing for the development of new and diverse applications.
Near Net Shape
Powder metallurgy components and products do not require extra processing. Each portion is nearly net form, which means it won’t need to be finished. Furthermore, powder metallurgy components offer extremely high dimensional precision.
Raw Materials
The supply of raw materials is a continual issue for manufacturing processes since a lack of resources can cause output to stall or stop. Powder metallurgy raw materials are widely available and reasonably priced. Powdered metals are highly common materials that are widely accessible from a variety of manufacturers. As the popularity of powder metallurgy has expanded, an increasing number of providers have created fabrication procedures to satisfy the demand.
Repeatability
It is critical in mass manufacturing that every part, from the first to the last, meets the dimensions specifications of its design. Degradation happens during manufacturing in specific procedures, resulting in flaws and variances in the individual pieces. The powder metallurgy process’s homogeneity and reproducibility prevent such mistakes and ensure that every item has precise dimensions.
Wear Resistance
To minimize costly repairs and replacements, it is critical that parts placed in vehicles, aircraft, and machines have a long life lifetime. Powder metallurgy produces parts with superior wear resistance and friction coefficient. These criteria ensure that a powder metallurgy item will survive for a long time.
Magnetism
Powder metallurgy is distinguished by its capacity to mix various metals to build and construct magnetic components while also controlling their magnetic characteristics. Because powder material compaction is the same method used to generate magnets, it is a simple attribute to include in powder metallurgy components.
Chemical Homogeneity
When a material is homogenous, its composition is the same no matter where in the substance the sample is taken. This attribute indicates that a part’s qualities are constant across its structure. Chemical homogeneity is required for a component to be consistent, strong, and durable. This is a feature shared by all powder metallurgy products, and it is the reason to endure so long.
Disadvantages of the Powder Metallurgy Process
The disadvantages of powder metallurgy process are
- The metal powder has high initial starting cost.
- Due to the huge presses necessary to achieve the appropriate compressing pressure, the size of the pieces produced is limited.
- The operation’s equipment is expensive.
- It is impossible to have a totally dense product.
- Metal powder is costly and, in certain cases, difficult to store.
- The dies used must be highly accurate and able to bear high pressure and temperature.
- The ductility of the parts produced is low.
- The challenge of sintering low melting powder.
- The requirement for protected environments.
Applications of the Powder Metallurgy Process
The applications of powder metallurgy process are vast and they are
- Automotive Gears
- Jet Engine Turbine Disk
- Surgical Tools
- Gears
- Oil and Gas Industry
- Tools
Automotive Gears
The usage of powder metallurgy in the production of vehicle components is closely tied to advancements in novel material development and pressing technology. The capacity to generate complicated configurations utilizing cost-effective manufacturing processes is one of the benefits of powder metallurgy for car parts production. The ability to produce complicated components with little waste or trash eliminates the need for finishing or machining.
The most common powders used in the manufacture of car components are iron-based and stainless steel powders. Some of the produced components are as follows:
- Steering components
- Transmission components
- Connecting rods
- Main bearing caps
- Variable valve timing
- Seating applications
- Exhaust applications
- Catalytic reduction system
- Fuel system components
- Engine components
Jet Engine Turbine Disc
Aerospace Turbines must be able to tolerate severe temperatures and pressures. The turbine disc is the central component to which engine fans, compressors, and turbine blades are attached. Turbine discs are composed of high-temperature alloys that fulfill the appropriate grades and standards. Turbine discs are machined and polished to provide maximum performance.
Turbine Discs are made using atomized powders and hot isostatic powder metallurgy. Because it is vital to avoid the entrance of undesired particles or pollutants, the procedure is intricate and difficult.
Surgical Tools
Surgeons demand precision instruments that function admirably. To satisfy strict requirements, blades must be polished to the finest point and ground. Graspers, which are meant to aid in endoscopic procedures, are a few millimeters long with a complicated design that must be stretched before shipping. A knot pusher is a type of grasper that has the same size and specifications as a grasper.
Gears
When it comes to powder metallurgy, gears are one of the most regularly manufactured items. Powder metallurgy, as manufacturers have discovered, provides superior precision, resulting in extended gear life. Gears with blind corners can be manufactured, avoiding the necessity for undercut relief.
Powder metallurgy allows gears to readily integrate with other components such as cams, ratchets, and other gears. Powder metallurgy can make any type of gear, including helical and involute gear shapes.
Oil and Gas Industry
Exploration for Gas and Oil necessitates the use of hard metal and diamond cutting equipment. Powder metallurgy creates tools composed of austenitic and stainless steel to suit the need. Valves and manifolds are built to exact dimensions and specifications using materials that can withstand severe, dangerous, and stressful environments.
Tools
Hand tools for Do It Yourself (DIY) tasks and lawn maintenance are fast developing market products of powder metallurgy makers. Powder metallurgy’s precision, accuracy, and result in tools that last five times as long as those manufactured by conventional methods. Powder metallurgy tools provide
- High Wear Resistance
- Remarkable Toughness And
- Enhanced Hardness Retention.
Conclusion
Powder metallurgy is an old, unique technique for forming shapes and patterns using ferrous and non-ferrous metals with greater correctness and flexibility. Despite the fact that there are few constraints to the use of metals in this process, it has progressively developed to become a key aspect of the industrial industry’s manufacture of a broad variety of parts and products. Powder metallurgy is a fantastic choice for manufacture of gears that require complicated forms and tolerances, but it falls short in terms of strength. As a result, manufacturers are including more Powder metallurgy gears in their designs, including novel alloys and powder metal processing processes.