What is Electrical Discharge Machining?
The Electrical Discharge Machining is a type of Non-Conventional Machining Process or Non-Traditional Machining Process. As this is a material removal process, we can also say that it is a Type of Machine Tool. Additionally, the Electrical Discharge Machine is also called as Spark Machining Process, Spark Eroding, Wire Burning (or Wire Erosion), and Die Sinking Process. The machine that does the Electrical Discharge Machining using a Dielectric Fluid is called as Electrical Discharge Machine, which is shortly called as EDM.
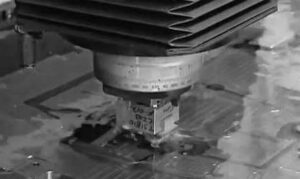
The Non-Traditional Machining Process plays an important role in machining the materials where the Normal or Traditional Machining Method or Conventional Machining Process cannot. Few of the Conventional Machining Processes are
As the name indicates, it works on Electricity, which develops an electrical spark to machine (or cut) the materials according to our required design or required shape irrespective of the material’s hardness. The Intensity or Current that require to cut the material depends upon the type of material, thickness of material, and its properties. The materials that are used in advanced applications like Aircrafts, Aero-Planes, Rockets, etc., are not machined or shaped using the Traditional Machining Methods, which demands higher finishing, micro cutting, etc.
Also Read:
- Ultrasonic Machining Process – Parts, Types, Working, Advantages, Disadvantages, Applications – FAQ’s
- Water Jet Machining Process – Parts, Working, Advantages, Disadvantages, Applications – FAQ’s
Parts of Electrical Discharge Machining:
To run any device of machine and machine tool, the parts plays a major role. Accordingly, the parts of Electrical Discharge Machining too consist number of parts which are very important. Observe the parts of the EDM in the above image.
- Pulse Generator (Power Supply)
- Workpiece
- Fixture
- Dielectric Fluid
- Pump
- Filter
- Tool Holder
- Spark generation
- Tool
Pulse Generator (Power Supply)
The Pulse Generator is a power source to the whole Machine, the power is given to the EDM system i.e. Negative Terminal is given to the device and a Positive Terminal is given to the workpiece.
Fixture
The fixture is used to hold the workpiece steadily well in a dielectric box.
Dielectric Fluid
This type of Fluid is a type of Hydrocarbon or Mineral Oils, which the workpiece is placed and machined. At everyday conditions, this type of fluid acts as an insulator. In this sense, no electric conductivity is taking place.
Pump
The Pump is the electronic device or motor that will help to deliver or discharge the fluid continuously into the dielectric container. The type of pump depends upon the application, capacity, etc.
Tool Holder
The Tool Holder is the holding device that will steadily catch the Electrode.
Tool
In the Electrical Discharge Machining Process, the Electrode that is moved against the workpiece is the Tool, which produces the electrode spark to cut the material.
Working of Electrical Discharge Machining:
The working of Electrical Discharge Machine Process looks simpler but the way of achieving the machining is complex.
- As we know, the when Positive Terminal and Negative Terminals called Anode and Cathode comes closer to each other will produce a spark or dielectric. According to this principle, the EDM will work. In the Spark Machining Process, the Positive Terminal called as Anode and Negative Terminal called as Cathode will be arranged; which means the workpiece will be connected to the Anode and Electrode (that produces the heat or spark) will be taken as Cathode.
- Now, the Electrode is forced against the workpiece, which the gap is almost 0.05 mm and due to this gap, the electrical spark produce and cut or remove the material from the workpiece. To make it more efficient and cool down the produced spark, the workpiece is placed in the Liquid Dielectric Material. The Liquid Dielectric Material may be Hydrocarbons or any other Mineral Oils.
- The electric discharge reasons severe heating of the material. The heating ends in the melting away of a few components of the workpiece. The liquid additionally assists in cooling in the course of the machining procedure.
Types of Electrical Discharge Machining Process:
There are three types of Electrical Discharge Machining Processes, which is divided according to its working process and devices. They are as follows
- Wire Cut Electrical Discharge Type
- Hole Electrical Discharge Type
- Die-Sinking Electrical Discharge Type
Wire Cut Electrical Discharge Machining
- The Wire Cut Electrical Discharge Machine is a type that makes use of CNC motion to provide the favored contour or form.
- It does now no longer require a unique fashioned electrode, alternatively it makes use of a continuous-travelling vertical Wire.
- The electrode in Wire Cut EDM is set as thick as a small diameter needle whose course is managed via way of means of the device to provide the form required.
Hole Drilling Electrical Discharge Machining
- As the name implies Hole drilling Electrical Discharge is used to machine or cut the holes. However, in comparison to conventional hollow drilling methods, this holes are extraordinarily small and deep that do not require deburring.
- This approach additionally makes use of the equal essential ideas as die-sinking EDM, Even though the holes are made with a pulsing cylindrical electrode that actions deeper into the workpiece because the wire is eliminated.
- This approach has been key to the development of high-temperature turbine blades, because it lets in for extremely difficult cooling channels to be synthetic within side the turbine blades.
Die-Sinking Electrical Discharge Machining
- Die-Sinking or Ram Electrical Discharge Machine is an alternative method to make the cavities.
- Firstly, a graphite electrode is produced with inside the opposite form to the desired hollow space to shape the die. The method works via way of means of inducing a voltage among the die and the electrically conductive workpiece at the same time as being submerged in a dielectric fluid.
- The die is slowly reduced in the direction of the workpiece until electric powered breakdown takes place and an electrical spark creates between the `spark gap` or electrode and workpiece.
- This vaporizes/melts the wire, and the dielectric in the end includes the ejected debris away. Material is eliminated from the workpiece via way of means of a sequence of high-frequency spark, exactly slicing out the favored form.
Also Read:
- Spot Welding – Types, Parts, Working, Advantages, Disadvantages, Applications and More
- Arc Welding – Types, Parts, Working, Advantages, Disadvantages, Applications, and More
Advantages of Electrical Discharge Machining:
The Advantages of Electrical Discharge Machining are
- Hard Materials
It is used to machine (or cut) the hard materials like Diamond, Quartz, Boron Carbide, Tempered Steel, etc.
- Accuracy
In the Electrical Discharge Machining, the Accuracy of machining is high and achieves the targeted Tolerances.
- Complex Shapes
As Spark Machining Process is a type of Non Conventional Machining Process, it is used to machine the Complex Shapes.
- Internal Contours
The internal contours can be able to machine even up to Microns in the EDM.
- Contactless Machining
Due to the contactless machining, the Electrical Discharge Machine will not harm or destroy any soft or weak materials while machining.
- Surface Machining
It is good and high surface finishing can be achieved by EDM.
- Non-Conductive Materials
The EDM is also used to machine or cut the Non-Conductive Materials also, which increases its area of application.
Disadvantages of Electrical Discharge Machining:
The Disadvantages of Electrical Discharge Machining are
- Cost Effective
As the EDM is Non Conventional Machining Process, which is used in machining high materials so, it is cost effective.
- Material Removal Rate
The Material Removal Rate in Electrical Discharge Process is low.
- Hazard
Due to the usage of Dielectric Materials, EDM produces few fire hazards which is one of the drawbacks but can be prevent with few precautions.
- Power Consumption
As the whole process works on electricity, the power consumption is high and increase the electrical charges (depends upon its working duration).
- Non-Conductive Materials
The Non-Conductive Materials can also be machined but require change of set-up or few devices.
- Tool Wear
To produce the electrical spark and achieve the machining, the EDM Tool Wear is high
Applications of Electrical Discharge Machining Process:
The Applications of Electrical Discharge Machining Process are
- Small hole drilling
The Spark Machining Process is mostly used to cut the materials with small diameters (it may be up to microns too).
- Injection molding
It is also used mostly in Mold making and dies making like Coinage.
- Aerospace Industries
The Electrical Discharge Machining process is mostly used in the manufacturing of the Aerospace Components, and Devices.
- Dissemble of Components
Not only manufacturing, but also Spark Machine will help in dissembling of the components that are costlier without destroying their whole component.
Conclusion:
It is not a possible way to machine or cut and remove the all types of materials by using only one machine. The materials machining will depend upon the requirement, shape, thickness of workpiece, and a lots of factors. Similarly, Electrical Discharge Machining is evolved according to its specific factors. Therefore, it is called as the Non-Conventional Machining Process or Non-Traditional Machining Process.
Frequently Asked Questions:
What are the types of Electrical Discharge Machining?
There are three types of Electrical Discharge Machining Process, they are as follow
- Wire Cut Type
- Hole Type
- Die-Sinking Type
What is the purpose of using Electrical Discharge Machining Process instead of other types?
Not every type of material factors like hard, soft, ductile, brittle, high thickness, low thickness, shape, etc. able to machine by single type of machining process. So, the usage of every machine tool depends upon the factors of the workpiece. The purpose of Electrical Discharge Machining Process is that it can machine hard materials and intricate shapes
What is the Dielectric Fluid used in the EDM process?
The Dielectric is a type of insulator that increase the efficiency of the machining and prevents in increasing the heat while machining the process. The type of Dielectric Fluid used in the Electrical Discharge Machining Process is either Hydrocarbons or Mineral Oils.
What type of materials are used to machine using the Electrical Discharge Machine?
The Electrical Discharge Machine is used to machine or cut the materials like
- Hard Materials like Tempered Steel
- Diamond
- Quartz
- Boron
- Carbide, etc.
Is Material Removal Rate high in Electrical Discharge Machining?
No, the Material Removal Rate in the Electrical Discharge Machining Process is not high, which is low due to the limitations of the process.