What is a Gear Hobbing Machine?
A Gear Hobbing is a type of Manufacturing Process and type of Machine Tool that produces the different types of Gears like Spur Gear, Helical Gear, etc. The Machine that produces the teeth on Spur Gears, Worm Gears, Helical Gears, Cutting Splines, and Cutting Sprockets using a Spinning, MultiPoint Cutting Tools is called as Gear Hobbing Machine and the splines that cut the gears is called as Hob. This is a type of Gear Forming Process. Although this hobbing Tool (or Hobbing Cutter) cuts constantly and creates precised gears at high production rates, hobbing is used to cut more gears than traditional or general techniques.
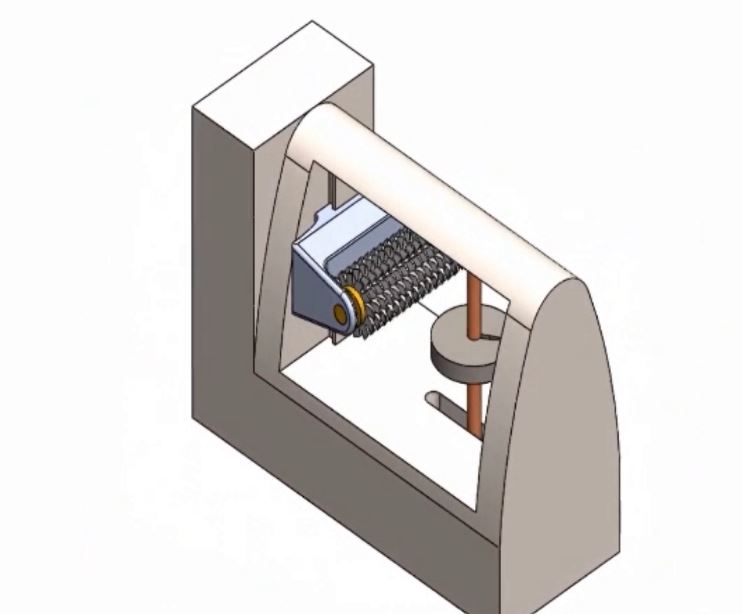
Gears can also be created in gear-making facilities by Grinding, or a combination of cutting and Grinding Processes.
The majority of cut gears manufactured in significant quantities are made on machines that use the gear-generating process. This approach is based on the idea that two Involute Gears, or Gear and Rack, which having exact similar diametrical pitch. As a result, a gear or rack-shaped cutting tool can be used to cut gear teeth in a gear or rack blank. This technique is employed in the design of a variety of commonly used generating gear-cutting devices. Gear shapers are gear-generating devices that cut with reciprocating strokes.
Also Read:
- Whitworth Quick Return Mechanism – Parts, Working, Working Video, Advantages, Disadvantages, Applications and More
- Crank and Slotted Lever Mechanism – Parts, Working, Advantages, Disadvantages, Applications and More
More About Gear Hobbing
A hob in Gear Hobbing Machine, also called as Hobbing Gear Machine is similar to a worm gear; whereas, it has several flutes around its periphery that run parallel to the axis to generate cutting edges. To create the teeth, the hob is turned and fed against a revolving gear blank.
By this process, the hobbing can make spur, helical, and worm gears, as well as splines of any type of material (ferrous and nonferrous metals and polymers), but not bevel or internal gears. Whereas traditional hobbing cannot achieve high accuracies (High Tolerances) and requires extra finishing processes if high precision is desired. Its versatility and simplicity make it a cheapest process of cutting gears.
Types of Hobbing Process
There are three types of Hobbing Process according to their cutting angle. They are
- Axial Hobbing
- Radial Hobbing
- Tangential Hobbing
Axial Hobbing
The gear blank is brought near to the hob to acquire the required tooth depth, then the rotating hob is fed straight to the surface of the gear blank. The Axial Hobbing Process is a used to cut Spur Gears and Helical Gears.
Radial Hobbing
The hob and gear blanks are positioned with their axes normal to each other in this process. The spinning hob is pushed against the gear blank in either a radial or perpendicular direction to the axis of the gear blank. Due to its radial hobbing, this type of hobbing is used to produce the Worm Wheels.
Tangential Hobbing
It is also used to cut teeth on a worm wheel. In this scenario, the hob is held horizontally but at a right angle to the blank’s axis, which is called as Tangential. To cut the teeth, initially fix the hob to the complete thickness of the tooth and then feed it ahead axially tangential to the surface of the gear blank.
Types of Hobs
There are different types of Hobs according to the various aspects, they are as follow
- Roller Chain Sprocket Hob
- Worm Wheel Hob
- Involute Spline hob
- Chamfer Hob
- Straight Side Spline Hob
- Chamfer Hob
- Straight Side Spline Hob
- Serration Hobs
- Semi-Topping Gear Hob
Let us read about these types of hobs in detail
Roller Chain Sprocket Hob
This type of hob is the most commonly using hob, which operates along the chains formed by rollers interlinked by pins. These chains form the gaps that the sprocket’s teeth fit into in order to transfer movement energy.
Worm Wheel Hob
Worm Wheel Gear Hob is designed for plunge cutting which is manufactured in a shell or shank with a straight or spiral gash. These gear hobs match the worm shaft with a sharpening cut.
Involute Spline Hob
They have straight sides teeth like a gear hob, and are usually of stub tooth depth which are Types of Gear Hobbing Machine manufactured in single or multiple thread designs, with diametral inclination ranging from 2.5/5 to 128/256 and pressure inclined at 30°, 37.5°, or 45°.
Chamfer Hob
The Chamfer Hob looks similar to a standard gear hob but with asymmetric teeth in which one flank is used for cutting the chamfer, the other flank is used to not touch the counter flank. Chamfer angles are around 15-30 degrees on obtuse edge, 25-45 degrees on acute edge.
Straight Side Spline Hob
Straight Spline Hobs are used for cutting parallel splines and are manufactured with or without lugs, semi-topping, and shoulder clearance types in Class ‘AA’ & ‘A’. We have picked up the ability in offering a better quality scope of Spline Hobs than the regarded clients.
Serration Hob
They are used to cut serrations as per requirement in automobile industries, specifically designed for machine gears, sprockets, and splines, which are used as a hobbing cutter.
Semi-Topping Gear Hob
This hob is used to eliminate the sharp corners between the tooth flank and outside diameter.
Types of Gear Hobbing Machines
There are different types of Gear Hobbing Machines or Hobbing Gear Machine according to its construction and process of machining. They are as follow
- Vertical Gear Hobbing Machine
- Horizontal Gear Hobbing Machine
- CNC Gear Hobbing Machine
Vertical Gear Hobbing Machine
Vertical gear hobbing is the most flexible and widely utilizing type of Gear Hobbing Machine. In this type, the axis of the Hob is perpendicular to the machine’s bed while cutting or machining. Such alignment of hob to the bed is called as the Vertical Gear Hobbing Machine.
Horizontal Gear Hobbing Machine
Horizontal type of Hobbing Gear Machine is often used to cut long workpieces. If the operation axis is parallel to the machine’s bed, then it is called as Horizontal Gear Hobbing Machine.
CNC Gear Hobbing Machine – Direct Drive
The type of Gear Hobbing Machine, which has a direct drive Spindle and Table is called as CNC Gear Hobbing Machine (Direct Drive). Because the spindle and table are directly linked to the rotor of the Servo Motor, due to this, the mechanical transmission mechanisms such as Gearboxes and Worm Gear Drives are not required. This results in unrivaled precision, which mechanical transmission elements cannot attain.
Construction of Gear Hobbing Machine
- The gear blank workpiece is allowed to spin in the machine with a spinning cutter known as a hob during the gear hobbing process. The gear hobs are a Multipoint Cutting Tools that is used to accomplish the gear hobbing procedure.
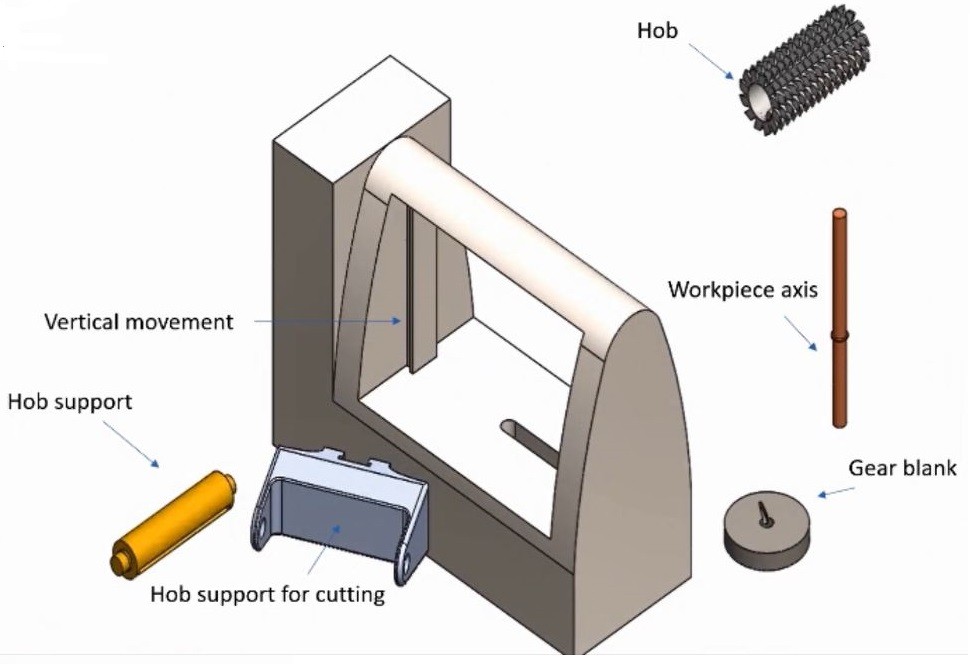
- The Gear Hob or Hobbing Gear Machine is designed to resemble a Worm Gear, with many straight flutes running parallel to its axis all around its circle. These flutes are shaped by applying correct angles so that they can function as the Cutting Edges of a Multipoint Cutting Tools.
- During the Gear Hobbing Operation, the Multipoint Cutting Tools or Gear Hob Tools are steadily rotate at a consistent RPM (Revolutions Per Minute) while being fed to the gear blank workpiece.
- The Gear Blank Workpiece is also kept spinning at all times. Both the RPM of the gear blank work-piece and the RPM of the gear hob cutting tool is synchronized exactly per each revolution of the gear hob, the gear blank spins by a particular distance to one single pitch distance of the gear being cut.
- The action of both the Gear blank and the Gear Hob is continuous and consistent.
- The gear cutting hob’s teeth act similar to screw threads, with a set of Helix Angle.
- Gear Hobbing is a sort of Mechanical Metal Forming procedure used to create a broad range of Gears such as spur gears, helical gears, hearing-bone gears, splines, gear sprockets, and among others.
Aslo Read:
- Pipe Bending Machine – Parts, Working, Advantages, Disadvantages, Applications and More
- Hand Water Pump – Parts, Working, Advantages, Disadvantages, Applications and More
Working of Gear Hobbing Machine
- Gear Hobbing Machine (or Hobbing Gear Machine) is a Machining Technique for making gears that include concurrently rotating the gear blank workpiece and the cutter known as a hob with a perfect gearing ratio connecting the hob and the gear blank work-piece. The gear blank workpiece is repeatedly fed into the spinning hob in this gear hobbing process until the appropriate depth of cut is obtained. The hob is then continuously fed across the blank’s face until all of the teeth are cut.
- The hob teeth of spur gears are placed in a Parallelly to the axis of rotation of the Gear Blank. To generate the correct helix, the axis of the hob is positioned over an angle with the gear blank during the helical teeth hobbing procedure. When making of worm gears, the hob’s axis is set at Right Angles to the gear blank workpiece.

- When compared to other gear producing and machining processes, the gear hobbing method has a very high rate of output. This procedure may be used to make many sorts of gears such as spur, helical, worm gears, sprockets, splines, and so on. However, the rotary cutter used in the cutting procedure, which cuts up to the shoulder, this is not feasible.
Advantages of Gear Hobbing Machine
The Advantages of Gear Hobbing Machine are
- Speed – Some gear manufacturing procedures are time-consuming but the Hobbing Gear Machine is a quick operation. As the machine is totally dedicated to produce Gears, it does not require much operating care, and we may stack many units to hob them all at the same time for producing some gears.
- Precision – Unfortunately, everybody cannot use a hobbing machine. Hobbing may be exceedingly exact with the correct competence, which is resulting in high-quality gears. This speed is achieved without sacrificing the precision or quality of the finished product.
- Flexibility – There are several ty pes of hobs, as well as several types of hobbing machines too, due to this, several varieties cater to niche applications, so you will always have alternatives.
- Simplicity – Hobbing Gear Machine is simple to use and can generally hob numerous pieces at the same time, if they are placed on top of one other. Furthermore, hobbing machines require relatively little maintenance or operational care when in use.
- High-Volume Production – They enable high-volume production with shorter turnaround times than most other methods.
Disadvantages of Gear Hobbing Machine
The Disadvantages of Gear Hobbing Machine are
- The Gear Hobbing Machine is not used to produce Internal Gears.
- The restricted neighboring shoulders are greater than the gear’s root diameter.
- Splines and Serrations are incompatible with hobbing Gear Machine.
Applications of Gear Hobbing Machines
The Applications of Gear Hobbing Machines are as follows
- It is commonly utilized in the manufacture of Spur Gears, Helical Gears, Worms Gears, and Worm Wheels.
- Hobbing Gear Machine may also be used to make Internal gears, if the machine has the capability of installing relative head.
Conclusion
Gear Hobbing Machine is the most common method of producing gears. Furthermore, to remain competitive in the industrial market both nationally and worldwide, producers must create the greatest possible quality at the lowest feasible cost. Quality, Productivity, and Tool life all influence the cost per piece. As a result, health monitoring or condition monitoring is critical for the Hobbing Gear Machine operation.
According to the literature study, the development of numerical and analytical models for modeling the gear hobbing process has remained a primary research focus to evaluate undeformed chip shape, cutting forces, and tool wear. However, vibrational analyses of gear hobbing machines receive far less attention.
Frequently Asked Questions:
What is a Hob?
Hob is one of the main and key parts of Gear Hobbing Machine. It has a cylindrical form and helical cutting teeth. These teeth feature grooves over the span of the length of the hob and help in chip removal and cutting. Special hobs are also available for certain gears such as spline and sprocket gears.
What is the difference between Gear Milling and Gear Hobbing?
In the Hobbing Gear Process, a helical cutting tool (hob) is used to gradually produce gear teeth. As the hob is fed over the face width of the gear blank, both the hob and the workpiece rotate continuously and machining take plcae.
In the Gear Milling Process, a revolving Multi Point Cutting Tool with a cross-section comparable to that of the produced teeth creates distinct tooth spacing. The gear is restored to its original position after each cut, and the gear blank is indexed for the next cut.
What is the difference between Gear Shaping and Gear Hobbing?
The shaping process use a reciprocating motion of the cutting head. Some Shaping Processes cut one tooth at a time, while others use Multipoint Cutting Tools revolving blade to cut teeth in numerous rounds. This is a tool that can be used to replace internal gear teeth. Gear Hobbing involves a rotating cutter (hob), which then rotates in relative speed with the part being hobbed. It is involved in cutting external spur and worm gears.
Gear Shaping Tooth is cut one by one while in gear hobbing, all tooth is cut simultaneously till the completion of the process. The gear shaping process provides good accuracy but it is time-consuming while gear hobbing is both accurate and saves time.
Is there any machine that can perform Gear Hobbing and Gear Shaping at the same time?
Yes, there are a number of machines. If you have a competent programmer to code the operation, a 3 axis machine center might be able to do it. With a holding fixture comprising one or two fixed locations that find and lock the raw blank of material each gear is built from, a multi-axis wire EDM (Electro-Discharge Machine) can also be used to complete the task in two procedures.
Which gear manufacturing method is mostly preferred in the industry?
Gear Hobbing is the mostly used procedure and manufacturing machine for Gear Cutting. In the circumstances, when Hobbing is not practicable, Gear Shaping is employed.
Which Type of Gears are produced using Gear Hobbing machine whether Helical, bevel, or spur gear?
Gear Hobbing or Gear Hobbing Machine can be used for cutting all the types of Gears. A face hob that is different from the standard gear hob is used to produce the bevel gear.