What is Ultrasonic Machining Process?
Ultrasonic Machining Process is a non-traditional machining process and subtractive manufacturing process. The working principle of Ultrasonic Machine is to remove material from the surface of materials by Ultrasonic Waves, which contains a high frequency of around 20000 to 30000 Hz and low amplitude oscillations of about 25-50 micron with a shaped tool using abrasive slurry against the material surface.
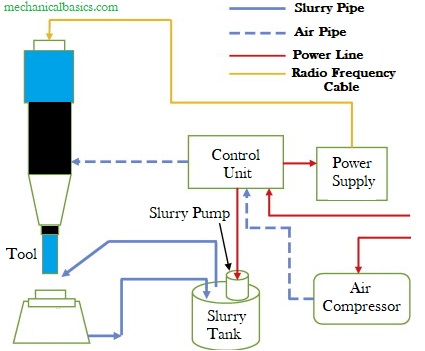
The abrasive slurry runs between the tool and the workpiece to perform the operation. Due to this, the tool and the workpiece never interact with each other (fragile workpieces can be conveniently used in USM) and the tool will have the same shape as the job to be machined.
Also Read:
- Milling Machine – Parts, Types, Working Principle, Advantages, Disadvantages, And Applications – FAQ’s
- Single Point Cutting – Nomenclature, Material, Types of Cutting Angles, Operations, Advantages, Disadvantages, And Applications – FAQ’s
Types of Ultrasonic Machining Process:
According to the construction and usage of chemical abrasives, the Ultrasonic Machining Process is of two types, they are
- Rotary Ultrasonic Vibration Machining
- Chemical Assisted Ultrasonic Machining Process
1. Rotary Ultrasonic Vibration Machining:
In Rotary Ultrasonic Vibration Machining Process, vertically rotating or oscillating tool is allowed to revolve about a vertical centerline (axis of the sonotrode). Instead of using an abrasive slurry, the tool is impregnated with diamonds that are used to grind down the surface of the part thus the material will be removed.
Normally, the Rotary Ultrasonic Vibration Machining Process is used to produce deep holes with high level of precision for machining advanced ceramics and alloys such as glass, quartz, structural ceramics, Ti-alloys, alumina, and silicon carbide.
2. Chemical Assisted Ultrasonic Machining Process:
Chemical-Assisted Ultrasonic Machining Process type (shortly called as CUSM) uses a chemically reactive abrasive fluid for the machining of material. It is used for machining of glass and ceramic materials. In this type, the hydrofluoric acid (an acidic solution) is used for machining. Thus, the material removal rate and surface quality can be improved greatly compared to traditional ultrasonic machine.
Parts of Ultrasonic Machining Process:
As we know, the material is removed by Ultrasonic Waves, which require electrical and electronic devices to generate them. So, the parts of Ultrasonic Machining Process are
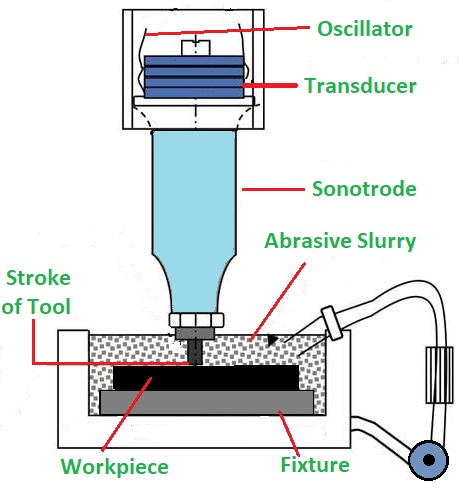
- Power Supply and High Frequency Generator
- Transducer
- Ultrasonic Amplitude Transformer Or Tool Horn
- Tool Holder
- Tool
- Cooling System
- Abrasive Slurry
- Pump
1. Power Supply and High Frequency Generator:
The process of Ultrasonic Machining requires an alternating current power supply to start the process. Generally high power sine wave generator is used because it converts low frequency (60 Hz) electrical power to high frequency (20k Hz). It is also Known as an Ultrasonic Power Supply or Electronic Oscillator.
The mostly used Frequencies are 20 to 40 kilohertz and these frequencies are supplied to electro-mechanical transducer.
2. Transducer:
In Ultrasonic Machining Process, the Transducer is used to convert the electrical energy to vibratory motion. There are two types of transducer and they are as follows.
- Piezo Electric Transducer
- Magneto-strictive transducer
Piezo Electric Transducer:
Piezo Electric Transducer type of Transducer generates a small electric current. Whenever the electric current is passed through crystal in the Ultrasonic Machining Process, the transducer will compress and expands. When the current is removed, crystal attains its original size and shape. The Piezoelectric transducers can be used for up to a power of 900 watts and these Piezo electric crystals (materials such as quartz or lead zirconate titanate) consists of high conversion efficiency of almost 95%.
Magneto-strictive transducer:
The magneto-strictive transducers are constructed using nickel, permalloy (consists Ni 45% and Fe 55%) or permedur (consists Co 49%, Fe 49% and V 2%) plates. When they are exposed to strong magnetic field, the change of length takes place. These are more rugged than the piezoelectric transducers and can be used for higher power capacity up to 2400 W.
However, their conversion efficiency is low, which varies between 20% to 35% and hence get heated when working of Ultrasonic Machine.
3. Ultrasonic Amplitude Transformer or Tool Horn:
It is also Known as tool concentrator. It virtually transmits the energy and amplifies the amplitude of vibration, which focuses the vibration towards the tool tip.
4. Tool Holder:
Tool Holder is used to hold and connects the tool to the transducer. Tools are connected to the lower end of the tool horn either by welding or screwing or soldering or brazing, which helps in removing materials.
5.Tool:
Every machining process do consist a tool and even the Ultrasonic Machine Process also. The type of tool used in ultrasonic machining should be indentation by abrasive particle, which does not lead to brittle fracture. Therefore, in Ultrasonic Machine, the tool is made of ductile materials like steel, stainless steel etc., which possess tough and strong properties. Additionally, the tool shape is same as the cavity needs to be created on the workpiece surface.
6. Cooling Mechanism:
As the process is going on, the whole system will develop the heat, so to cooling purposes during Ultrasonic machining process, a system is present on top of the transducer where we have a casing around the transducer and cold water entered from it and receive the heat from the transducer and escape through the exit.
7. Abrasive slurry:
Water based slurry of abrasive particle is used in Ultrasonic Machining Process. Hard abrasive particles like silicon carbide, and boron carbide are used in this slurry. Abrasives are applied at the site of machining and due to the pressure, the material from workpiece will be removed.
There are four types of abrasive slurry are used and they are Aluminum Oxide, Silicon Carbide, Boron Carbide, and Diamond Dust.
8. Pump:
The Pump is one of the Ultrasonic Machining Process parts and it is also called as Abrasive Gun, which is used to supply the abrasive slurry in between tool and workpiece interface under a definite pressure.
Working of Ultrasonic Machining Process:
The working process of Ultrasonic Machining is as follow.
- The transducer and sonotrode are attached to the control unit and now low frequency AC power is supplied to the high-frequency generator. Then the generator converts it into high frequency current, which varies in between 18 kHz to 40 kHz.
- Now, this high frequency alternating current is supplied to the transducer and the transducer converts this alternating current into mechanical vibration. The transducer starts vibrating longitudinally by magneto-striction and transmits this mechanical vibration to the sonotrode, which is attached to it through a mechanical focusing device called Velocity transformer.
- When this vibrating sonotrode strikes the surface of material with light force (so that there is enough space for the slurry to flow between the tool and the workpiece) and allowing the abrasive slurry to flow through between tool and workpiece interface, which further removes the material. The slurry flows in between the tool and workpiece and helps in the removal of the material from the surface.
Advantages of Ultrasonic Machining Process:
The advantages of Ultrasonic Machining Process are
- Ultrasonic Machine is used to machine brittle, non-conductive, Hard and Fragile material, which are often difficult to machine.
- It can be used for drilling the both circular and non-circular holes, which are made up of materials like carbide, ceramics, etc with high precision.
- It is capable of producing high tolerance parts.
- It is also used in machining the drill tool, dies, wire drawing machine etc.
- It is simple in operation and requires less time to machine. Moreover, its operation is noiseless too.
- No change observed in the physical properties of the material during the process, which is one of the main factor in Ultrasonic Machining Process advantages.
- Due to the development of less heat, Ultrasonic Machining Process can be used for workpiece sensitive to thermal fluctuations.
- Ultrasonic Machine is used to cut diamonds in industries.
- Even the unskilled operators can be able to operate the machine.
- Moreover, this machining type is Economical too.
Disadvantages of Ultrasonic Machining Process:
The disadvantages of Ultrasonic Machining Process are
- The Material Removal Rate is very low in Ultrasonic Machining Process.
- Ultrasonic Machining disadvantages consists consumption of high power.
- Ultrasonic Machining Process can be used only when the hardness of workpiece is more (softer Materials are difficult to machine).
- Ultrasonic Machining is limited to the machine’s surface of a small size.
- Tool Wear is Very high compared to other types of non traditional manufacturing process and Tool life is short.
- It is very difficult to drill the deep holes using Ultrasonic Machining Process.
Application of Ultrasonic Machining Process
The application of Ultrasonic Machining Process are as follows
- Ultrasonic Machine is used for the Machining of non-conductive ceramics, which cannot be machined by Electro Chemical Machining or Electrical Discharge Machining processes due to poor conductivity.
- It is Used for fabrication of silicon nitrite turbine blade.
- Ultrasonic Machining application can be observed in making of dies.
- Ultrasonic Machining Process is Used for wire drawing, blanking operations, and punching purposes.
Conclusion:
The Ultrasonic Machining Process is one of the types of non-conventional type that can be used for machine the both conducting and non-conducting type of materials. There are different types of traditional processes, which are limited in its applications and not able to machine the hard materials. So, the USM will be a great choice to choose and machine such materials. Furthermore, the finishing of materials is high and precise compared to other types.
Frequently Asked Questions:
1. What is Subtractive Manufacturing Process?
The Subtractive Manufacturing Process is a type of constructing or developing the products by removing the material from the workpiece using any tool. The objects will be 3D products.
2. Why USM is future of manufacturing?
The Ultrasonic Machining Process can be used for the Machining of non-conductive ceramics, which cannot be machined by Electrochemical Machining and Electrical Discharge Machining processes due to poor conductivity as well as for workpiece sensitive to thermal fluctuations because this machining process produces very little heat with less cost.
3. Why Ultrasonic Machining Process is a better option from other traditional process?
Ultrasonic Machining Process can be used to machine brittle, non-conductive material, Hard and Fragile material, which are often difficult to machine. Furthermore, it does not require much Skilled workers to operate and even semiskilled workers are more than enough.
As this process is best choice for working with hard materials such as ceramic matrix composites, piezo-ceramics, glass, ceramics, Quartz, ferrite, diamonds, alumina, PCD, sapphire, CVD silicon carbide, ruby, and similar ones so, it is the best option.
4. What materials can be used to make parts of Ultrasonic Machining Process?
The materials like steelwith high flexibility is good material choice to make the parts of ultrasonic machining
5. How the Ultrasonic Machining Process is related with frequency of transducer?
The transducer and sonotrode are attached to the control unit and a low frequency AC power is supplied to the high-frequency generator and this generator converts it into high frequency current. This high frequency alternating current is supplied to the transducer and then it converts this alternating current into mechanical vibration. Due to this, the transducer starts vibrating longitudinally by magnetostriction and transmits this mechanical vibration to the sonotrode. When this vibrating sonotrode strikes the surface with light force it removes the material form workpiece. By this way, the USM is related to with frequency of transducer.