What is CNC Machine?
Computer Numerical Control, simply called as CNC Machine, which is a type of machine tool. It is a computer controlled machine that performs numerous activities automatically with predefined code that employed or stored in and executed by the Machine Control Unit (MCU), a microprocessor connected to the machine. It is frequently used in manufacturing to machine metal and plastic products. CNC Machine is also called Subtracting Manufacturing Process, which is also count as a robot that follows a program. A computer is used to program or operate this type of automatic machine, which has a wide range of applications, including industrial automation.
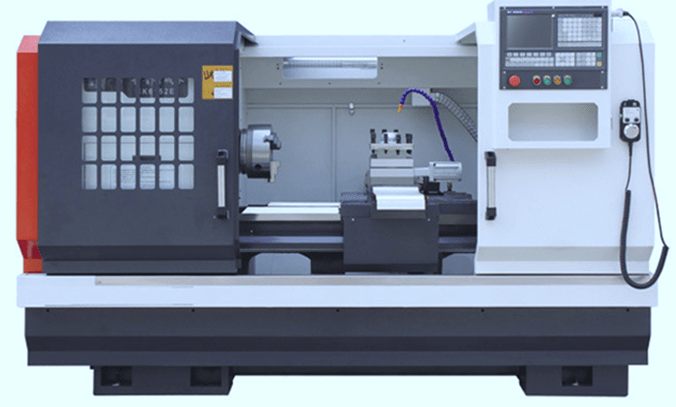
- CNC machines complete the work described by the numerical code entered into the machine.
- These codes are a collection of directives that the operator may use to tell the machine on what function to do. These are known as G-codes and M-codes.
- Each code has a specific purpose. Each program or code comprises the instructions and settings that the machine tool will use, such as the material feed rate, location, and speed of the tool’s components.
- Computer Numerical Control Machining is a production method in which industrial tools and machinery are moved according to pre-programmed computer software.
- The method may be used to manage a wide range of complicated machinery that includes Milling Machines, Lathe Machine, Router Machine, Grinding Machine, Lasers Machine, etc.
- It enables three-dimensional cutting jobs to be completed with a single set of commands. This implies that human operators are required to provide relatively minimal input.
- It is utilized in a variety of industries. It is particularly common in metal and plastic manufacturing.
Also Read:
Milling Machine – Types of Milling Machine- Its Working and Much More
Lathe Machine – Types of Lathe Machine – Their Working and Much More
Basic and Main Parts of CNC Machine
The Following are the basic and also the main parts of a CNC Machine.
- Input Devices
- Machine Control Unit (MCU)
- Machine Tool
- Driving System
- Feedback System
- Display Unit
Input Devices
These are the components that are utilized to program the component in the CNC machine. Punch tape readers, magnetic tape readers, and computers with RS-232-C connectivity are the three most often used input devices.
Machine Control Unit (MCU)
Simply, we can call Machine Control Unit as the brain of CNC machines. It controls the computer numerical control machine in all of its operations; the MCU’s numerous functions are listed below.
- It decodes the coded instructions that are given into it.
- To create axis motion commands, it employs interpolation (linear, circular, and helical).
- It sends axis motion commands to the amplifier circuits, which then drive the axis mechanisms.
- MCU gets position and speed feedback data for each driving axis.
- It handles auxiliary control operations like coolant or spindle on/off and tool changing.
Machine Tool
A CNC machine tool is always equipped with a sliding table and a spindle for controlling position and speed. The machine table is controlled in the X and Y axes, while the spindle is controlled in the Z axis.
Driving System
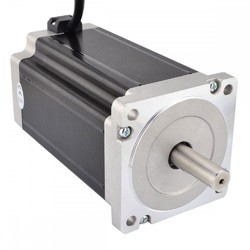
A CNC driving system is made up of
- Amplifier Circuits
- Drive Motors, and
- Ball Lead Screws
The MCU sends position and speed signals from each axis to the amplifier circuits. The control signals are then amplified (raised) in order to activate the drive motors. In order to position the machine table, the actuated drive motors move the ball lead screw.
Feedback System
The Feedback System of a CNC machine is made up of transducers that act as Sensors. It is often referred to as a measuring system. It is equipped with location and velocity transducers that continuously monitor the location and velocity of the cutting tool at all times. The MCU collects transducer inputs and analyzes the difference between the reference and feedback signals to generate control signals that rectify position and speed problems.
Display Unit
A monitor is used to display the CNC machine’s programming, instructions, and other essential data.
Types of CNC Machines
There are different types of CNC Machines, they are
- CNC Milling Machine
- CNC Lathe Machine
- CNC Router Machine
- CNC Plasma Cutter
- CNC Electric Discharge Machine
- CNC Laser Cutter
- CNC Water Jet Cutter
You will able to ready about all these types of CNC Machines in detail in the next article.
Quick Points on How CNC Machine Works?
The following diagram depicts the operation of a computer numerical control machine
- The component program is loaded into the CNC’s MCU.
- The MCU analyses all of the data and, based on the program, prepares and sends all motion orders to the drive system.
- The driving system responds to MCU motion directives. The drive system controls the machine tool’s motion and velocity.
- The feedback system captures the machine tool’s position and velocity measurements and sends a feedback signal to the MCU.
- The feedback signals are compared with reference signals in the MCU, and if mistakes occur, the MCU corrects them and sends fresh signals to the machine tool to be fixed.
- The display unit is where you can view all of your programs, instructions, and data. It functions similarly to the machine’s eye.
Working Principle of CNC Machine

- It is composed of two independent controls called CNC Controller that conducts activities such as program decoding interpolation, diagnostics machine actuation, and other functions. The Programmable Logic Controller (PLC) is another form of controller that regulates spindle on/off, coolant on/off, turret operation, and other operations.
- Slides are moved using their own Feed Drive Servomotors (AC or DC) or ball screws and nut drives. The feed drive controllers are in charge of the feed drive motors.
- Transducers that measure the sliding position have been installed on either the table or the motor.
- In addition, the position is monitored and confirmed using feedback transducers to assure positioning precision. The spindle is outfitted with AC or DC Stepped Motors.
- To alter the speed of the spindle motor, an appropriate control is utilized. The speed is monitored via an appropriate feedback device linked to the shaft.
CNC Machining Materials
- The CNC or Computer Numerical Control machining method is appropriate for a wide range of technical materials, including metal (e.g., aluminum, brass, stainless steel, alloy steel, etc.), plastic (e.g., PEEK, PTFE, nylon, etc.), Wood, Foam, Composites.
- The best material to use in a CNC manufacturing application is mostly determined by the individual manufacturing application and its parameters.
- Most materials may be machined as long as they have enough hardness, tensile strength, shear strength, chemical and temperature resistance to endure the machining process.
- The ideal cutting speed, cutting feed rate, and depth of cut are determined by the workpiece material and its physical qualities.
CNC Machine Programming
The CNC production is controlled numerically, with a software program specified to control an object. G-code is the language used in CNC machining to control the numerous aspects of a machine, such as speed, feed rate, and synchronization.
In essence, CNC machining enables you to pre-program both speed and location of machine tool activities and perform them in periodic, consistent cycles via software, all with little input from human operators. The computer code generated from a 2D or 3D design for CNC system to execute the machining process.
After generating the code, the operator runs it to check there are no errors in the code. Because of these characteristics, the method has been embraced throughout the industrial sector, with CNC manufacturing being especially important in the fields of metal and plastic manufacture.
Also Read:
Ultrasonic Machining Process – Its Parts, Working, Advantages, and More
Electrical Discharge Machining – Its Parts, Working, Advantages, and More
How Does CNC Programming Work?
CNC machining is primarily reliant on programming. A human programmer must enter the correct codes and confirm that they function properly. CNC machining is impossible without the codes. Most manufacturing machines are programmed to do one or two jobs. G-Code is far more complicated than this.
G-Code will regulate a wide range of CNC machine behaviour. Speed, Feed Rate, and Coordination are few actions that controlled by the coding. There is practically no need for human operators after G-Code is written and supplied into the machine. The code handles the majority of the operations for them.
Types of Software commonly used in the CNC Machining Process
Computer Aided Drawing (CAD)
Most CNC projects begin with CAD software. There are several CAD software programs available, but they are all used to produce designs. Popular CAD applications include AutoCAD, SolidWorks, and Rhino3D. There are also cloud-based CAD systems, and some include CAM capabilities or interact better with CAM software than others.
Computer Aided Manufacturing (CAM)
Computer Aided Manufacturing or simply CAM software is frequently used to build programs for CNC machines. Before the machine conducts any real cutting, users may create a “job tree” to manage workflow, specify tool trajectories, and run cutting simulations.
CAM applications are widely used as an update to CAD Software, generating g-code that informs CNC machines and workpiece moving components where to go. Wizards in CAM software make programming easier than ever. Some of the popular CAM software are
- Mastercam
- Edgecam
- OneCNC
- HSMWorks, and
- Solidcam
Advantages of CNC Machines
The advantages of CNC Machines are
- A Computer Numerical Control machine is capable of producing works with greater accuracy and precision than any other manual machine.
- It can run for continuous 24 hours a day.
- It produces pieces with the same precision. There is no variance in the manufacturing parts.
- It requires less area to operate.
- A semi-skilled operator can work and operate the machine with more accuracy and precision. It does not require a highly skilled operator.
- Changes and enhancements may be made quickly by operators, reducing wait time.
- It provides more operational security.
- It is capable of producing complicated designs with excellent precision in the shortest amount of time.
- The designer can imitate the manufacturer of his or her idea using sophisticated design tools. This eliminates the need for a prototype or model, saving time and money.
- A CNC requires fewer workers, which reduces labour expenses.
Disadvantages of CNC Machines
The disadvantages of CNC Machines are
- It is substantially more expensive than a manually controlled one.
- The initial investment is substantial.
- Computer Numerical Control machine components are expensive.
- In the case of CNC, maintenance expenses are much greater.
- It does not eliminate the necessity for high-priced tools.
- It necessitate the use of competent programmers.
- It is not appropriate for small-scale manufacturing.
- The expense of maintenance is higher.
Applications of CNC Machines
The applications of CNC Machines are
- The enhanced capabilities of CNC machines have simplified the job of numerous sectors. It is increasingly employed throughout the production industry due to its increased capabilities.
- They are built to deal with a broad variety of materials. Metal, glass, plastic, wood, foam, and composites are examples of such materials. We’ve used them to make anything from apparel to aeronautical components.
- They are used to make shafts, gears, square jobs, rounded jobs, rectangular jobs, threaded jobs, tapered jobs, milled jobs, drilling holes, and grooves, among other things.
- They are used in the fabrication industry to cut metal sheets.
- They are also commonly employed in the woodworking sector.
- Carving into the workpiece is also done with CNC.
Conclusion
CNC is a common way of producing components. Computer Numerical Control machines offer technology, precision, accuracy, and constant flow of processes required for high production rates. They have qualities that allow them to be quick with little to no human mistake. You can save time and money, as well as reduce the chance of material waste. Computer Numerical Control machines are quite complicated, and learning how to run one efficiently requires a significant amount of time and experience.
Although the majority of the codes are identical, CNC machines differ from one another. Its functioning does not necessitate any trouble. However, it must be handled by personnel with the necessary qualifications to guarantee that production runs smoothly on a daily basis.
Frequently Asked Questions
Which is superior 3D Printing or CNC?
The truth is that it is determined by the material, the intricacy of the part, and the economic forces at play. 3D printing technology, such as FDM machines, creates items from the ground up. They can produce complicated forms and interior components faster than a CNC machine. Conventional CNCs, on the other hand, are somewhat constrained by the tools available and the axes of rotation the machine may use.
While these machines can still be utilized with a range of materials, they are constrained by a pretty rigorous set of constraints and restrictions governing how they may interact with the various materials.
Is there another option to G-Code?
Yes. Many CNC machines can be programmed using specifically designed software. Individual firms create or change this programming to better fit their procedures.
Can you program and control CNC machines on your own computer?
Technically, if your computer possessed the necessary capabilities, you could utilize it. The majority of devices are offered in conjunction with a computer. It is strongly advised that you utilize those instead, but the decision is entirely up to you.
Is it necessary for me to be a coder in order to create CNC machine programming?
Before attempting to program CNC machinery, it is strongly advised that you get acquainted with fundamental coding. Technically, you don’t have to be a programmer. However, if you can collaborate with a computer developer, the procedure will be far more efficient and straightforward.