What Is A Milling Machine?
Milling Machine is a type of Machine Tool that uses the Multi-Point Cutting Tool (2 or more cutting edges or points) to cut and remove the material of the workpiece. It is a conventional or traditional (prevalent word) manufacturing process that can be found in every workshop and machining industry. Cutting the material and shaping the workpiece using a rotating tool (called multi-point cutting tool, one of the parts of milling machine) is called Milling, and the process is called as Milling Process.
Even though there are many types of milling machines, each type will be unique in its operation and working. However, the working principle is similar in all types, and their size and shape will differ according to their applications.
Also Read:
- Lathe Machine – Parts, Operations, Working, Advantages, Disadvantages, And Applications
- Water Jet Machining Process – Non Conventional Process – Parts, Working, Advantages, And Applications.
Parts Of Milling Machine:

The parts of milling machine will vary according to the type and application, but there are few parts common in every type of milling. A general and workshop miller that is used to perform grooving operation consist of following parts
- Base
- Column
- Knee
- Saddle
- Table
- Machine Vice
- Arbor
- Cutting Tool
- Motor
- Overhanging Arm
Base:
The Base is a supporting part of any type of machine tool where whole parts like the Knee, saddle, table, etc. and mounted on the Base. It is tough and observes all the vibrations of the milling while working. Mostly, the Base of the milling machine is made of cast Iron.
Column:
The Column is vertical and also a supporting component of miller. It is built hollow and acts as a housing for the driving mechanism and related components of the milling.
Knee:
The Knee is one of the parts of milling, which is a moving part fixed with an Elevating Screw (fixed between base and Knee) below it. The Table, Saddle, and Machine Vices are arranged over it.
The elevating screw is a height adjusting component that can move the knee up and down using manual effort on the handle. It can be used to adjust the whole setup according to the operator’s requirement and workpiece size.
Saddle:
The Saddle locates over the Knee and is a Horizontally Sliding Part of the miller. The table will be located over the Saddle and moves with respect to it. The movement of the Saddle is manual and able to slide using a Saddle Transverse Crank.
Table:
The Table is a long rectangular grooved part that rests over the saddle. The Table is horizontally sliding and a workpiece holding platform. The slots (T-slots, also called Machine Vice) over the Table will help the workpiece to hold it to proceed with the machining operation.
Machine Vice:
The Machine Vice is the workpiece holding device in the milling machine or milling process. As the milling process is performed by rotating the multi-point cutting tool, due to the motion of the tool, the workpiece will change its position, which is challenging to perform the task. So, to hold the workpiece tightly and firmly, the machine vice is used.
Arbor:
The Arbor is a cylindrical multi-point tool holder where the tool is fixed and rotate to perform the feeding and cutting operation. The Column and Overhanging Arm supports the Arbor. So, it can easily move the table (or saddle) up and down according to the requirement.
Cutting Tool:
The Cutting Tool is the crucial component of the milling where the material of the workpiece is removed using its cutting point or edges. The cutting tool of the milling process will differ according to the type of milling machine.

So, the type of milling machine cutting tool is a multi-point cutting tool. It can operate very quickly compared to a single-point cutting tool.
Motor:
It is a well-known fact that a Motor is used to convert electrical energy into mechanical energy. So, in the milling process, the motor is used to rotate the cutting tool (or multi-point cutting tool) to achieve the motion to shear the material and remove it.
Overhanging Arm:
The Overhanging Arm is one of the parts of miller where it is a metallic arm fixed to the Column at one end and free at another end. The Spindle or Arbor is connected to the overhanging arm.
Working Of Milling Machine:
The milling machine working is simple and requires manual efforts to operate it. Like Lathe Machine, the operator has to fix the tool, the workpiece using the transverse handles, and a motor will convert the electrical energy into mechanical energy.
Firstly, the multi-plate cutting tool is fixed to the Arbor using tool posts, the workpiece is held in the machine vice tightly. Then, the height of the saddle (or Table, or Knee) is adequately aligned properly according to the workpiece size so the cutting tool can feed over the surface to remove the material.
The driving mechanism is arranged in such a way that the motor is placed parallel to the axis of the cutting tool so, the Arbor can be connected directly to the motor, and energy (rotary motion) of the motor shaft can transmit to the Arbor and then to the Cutting Tool.
While the milling cutting tool is rotating, Table and the workpiece are moved over to the cutting tool (called Feeding) using the transverse handle.
Due to the feed and cutting tool rotation, the material is removed from the workpiece. Then, according to the requirement, the transverse handle is operated, and the workpiece is feed over to the cutting tool.
Classification of Milling Machine:
The classification depends upon the operation and type of multi-point cutting tool usage. Not each workpiece will be similar in shape and size; it will vary according to the application, so similar to its application the machining will vary, which may affect the milling process, and construction of the milling machine. There are different types according to their classifications, and they are
1. Column And Knee Type Of Milling Machine
- Vertical
- Horizontal
- Universal
2. Fixed Type Of Milling Machine
- Simplex
- Duplex
- Triplex
3. Special Milling Machine
- Rotary Table
- Tracer Controlled
- Pantograph
- Planetary
- CNC Milling Machine
- Drum
Column And Knee Type Of Milling Machine
i) Vertical Milling Machine:
The Vertical type is one of the types of millers that looks similar to the general type (or horizontal). The construction that differs from horizontal type are the Spindle, The Motor, Overhanging Arm, and Cutting Tool.
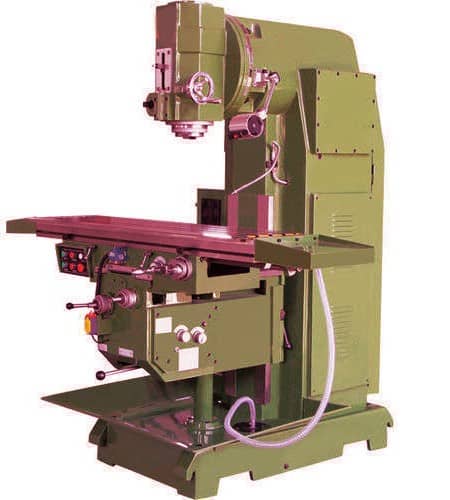
The Spindle in the vertical milling type rotates perpendicular to the Table and Parallel to the Column. As like Drilling Machine, the Vertical milling machine will be constructed. The Cutting Tool will rotate perpendicularly to the Table and Parallel to the Spindle.
ii) Horizontal Milling Machine:
The Horizontal Type of Milling is a general type of miller, and it is also called a Plain Milling Machine. Like the ordinary miller, the cutting tool (multi-point cutting tool) is fixed to an Arbor which is horizontal and parallel to the Table.

The Table can be operated in three directions that are vertical, horizontal, and cross directions to feed the workpiece against the cutting tool.
iii) Universal Milling Machine:

The Universal Milling Machine can move in four directions, whereas the horizontal type can only move in three directions. Therefore, the Universal Miller can be more advanced and perform several slotting operations by changing the attachments and fixtures like Lathe Machine Operation.
As with Vertical Milling Machine, the Spindle is vertical or perpendicular to the Table. The Table consists of Machine Wise, where the workpiece can be fixed and feed against the tool for operation. Furthermore, the Universal Miller can perform Bevel Gear, Spiral Gear, Spur Gear Cuttings, Twist, and Reamer cuttings by using different attachments and fixtures.
Fixed Type Of Milling Machine
i) Simplex Milling Machine:
A Simplex Type can perform basic operations. However, when it comes to the movement of the machine, which can move only in one direction. The construction of the milling machine is similar to the vertical type where the cutter is fixed to the Head or Spindle.
ii) Duplex Milling Machine:
As the name duplex indicates, the duplex machine is double-headed. It consists of two Spindles that rotate parallel to the Table (parallel to the earth’s surface). The Spindles constructed opposite to each other, with some space between them.

The Table is constructed between the two Spindles, and the workpiece can be held on the Table. The workpiece machining can be performed on both sides, which is faster and time-consuming. Due to its construction, it can be predicted that only large workpieces can be machined over it.
According to the size of the workpiece, the Spindles can be adjusted vertically or horizontally. So, it is convenient to perform the operation.
iii) Triplex Milling Machine:
The name Triplex indicates Three. As the name indicates, the Triplex Milling Machine is constructed with three heads and Spindles. In the Duplex Type, the Spindle is constructed on two sides of the Table. Similarly, the Triplex Miller consists of two Spindles on the right and left sides of the Table, and another will be constructed over the top of the Table. So, the workpiece can be machined over the top side also.

With the help of the Triplex Milling Machine type, the workpiece can achieve a good surface finish and faster machining process with accurate output.
Special Milling Machine:
i) Tracer:
The Tracer Milling Machine can trace the elements to perform the operation. This type of machine tool uses tracer control to copy the elements and produce them.
The complex and irregular shapes of milling operations can be performed over in this miller that is used in Automobile and Aerospace Fields.
ii) Pantograph:
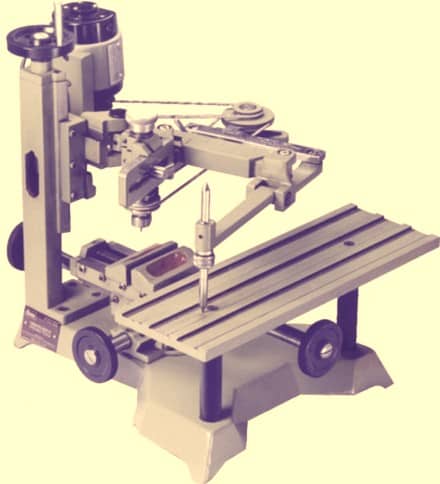
Pantograph Milling Machine is another type of miller that can generate replicate models. To perform the milling operation, the miller is pre-defined with the dimensions, shape, size, etc.
iii) Planetary:
In the Planetary Milling Machine the tool will perform the cutting operation by rotating around the workpiece. Accordingly, the workpiece can achieve a cylindrical shape.
iv) Drum:
Drum Milling Machine is another type of miller that consists of a drum-shaped cutter designed with cutting edges. The drum miller is constructed horizontally where the rotation of the drum can able to cut the workpiece.

This is a type of continuous process where the jobs are continuously machined one by one. Due to the large size, the drum is used to rotate at slow speeds.
v) Rotary Table:
The Rotary Table Milling Machine consists a rotary table that can rotate while performing a cutting operation. Like Vertical and Universal Types, the cutting tool is fixed perpendicular to the rotary table, and the table can be moved up and down (vertical direction) in directions to adjust and feed the workpiece over to the cutting tool.
The Machine Wise looks similar to the Chuck in the Lathe Machine, where the workpiece is centralized and fixed using Chuck.
vi) CNC Milling Machine:
CNC standards for Computer Numerical Control. The CNC is fully automatic, where the machine is coded according to the shape and size of the workpiece. Once the workpiece is entered into the machine, the whole process, like changing the tools, direction, speed, etc., is controlled by the machine itself.
The output of the CNC Miller will be a finished job with a good surface finish with accurate dimensions and quality.
Operations Of Milling Machine:
The main aim of this machine tool is milling and slotting, but due to the types, angle of usage, application, and flexibility of the milling, it can be used for different types of operations. The types of operations of milling machine are
- Plain Milling Operation
- Upward Milling Operation
- Downward Milling Operation
- Face Milling Operation
- End Milling Operation
- Gang Milling Operation
- Straddle Milling Operation
- T-Slot Milling Operation
- Groove Milling Operation
- Side Milling Operation
- Gear Milling Operation
Plain Milling Operation:

The Plain Milling Operation is one of the types of milling operation where the material on the surface of the workpiece is removed to achieve a smooth and plain surface.
Upward Milling Operation:

Upward Milling is a type of milling operation where the cutting tool is fed against the workpiece for machining or milling. It means, if the cutting tool is moving in a clockwise direction, then the workpiece moves horizontally right side.
Downward Milling Operation:
Downward Milling is one of the operations of milling machine where the cutting tool is feed along with a workpiece for machining or milling. It means that if the cutting tool moves in a clockwise direction, the workpiece moves horizontally right side.
Face Milling Operation:

This is a type of operations of milling machine. The process of milling the face of a workpiece is called Face Milling Operation.
End Milling Operation:
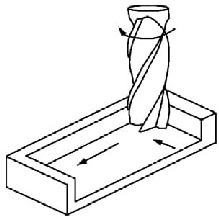
The process of milling the edges of a workpiece is called Edge Milling Operation.
Gang Milling Operation:

Gang Milling is another type of operations that uses two cutting tools (or cutters) to machine the surfaces of the workpiece. The two cutting tools (or cutters) are fixed on the same Arbor or Spindle so, the two cutters can run at the same speed. The cutting tools may be angular, stepped, and slotted.
Straddle Milling Operation:

The Straddle Milling Operation looks similar to the Gang Milling Operation, whereas it uses two cutting tools to machine the opposite sides of a workpiece. Like Gang Milling Operation, the cutting tools are fixed to the single Arbor and Spindle to rotate and perform the operation. This type of operation is chosen to machine a workpiece in a single pass or single cut.
T-Slot Milling Operation:

The T-Slot milling operation is another type of milling operation used to perform T-shaped slots using the T-Slot Cutter.
Groove Milling Operation

The milling operation that is one of the operations of milling machine used to perform grooves over the workpiece is called Groove Milling Operation.
Side Milling Operation:
Side Milling Operation is a primary type of milling operation used to flatten the sides of a workpiece.
Gear Milling Operation:

The Gear Milling Operation that is used to produce the Gears. A cutter is a feed over to the workpiece to cut teeth on the sides. Once the teeth are machined, the process repeats to cut the other teeth and continues until the gear is produced or whole teeth are machined.
Advantages Of Milling Machine:
The Advantages of Milling Machine are
- Due to the use of the Multi-point Cutting Tool, the operation is quick and stood at one of the main advantages of the milling.
- The Standard Milling can offer an excellent surface finish.
- When it comes to the CNC and other computer operating milling, the productivity is high.
- The operation involves less human effort in the entire operating process.
- The Milling Process on Standard Milling Machine is cheaper.
- Due to its movements, the working process is flexible and accessible.
- Milling can be customized according to the requirement of the working operation, which resulted in several types.
- The size of a milling is not as large as the lathe machine so, it can be enough to set up in a small room.
- The maintenance of the miller is easy and does not involve high-risk management.
Disadvantages Of Milling Machine:
The Disadvantages of Milling Machine are
- Due to the limited operating process, it cannot be used to perform other operations like Threading, Knurling, Drilling, Broaching, etc.
- As the operation gets complicated, there is a requirement for high-level milling machines, which is cost-effective.
- The difficulty of operation increases according to the workpiece operation. So, it demands high-skilled labour.
- The increase of speed leads to Tool Failure.
Applications Of Milling Machine:
The Applications of Milling Machine are
- The Standard Miller is mainly used to perform slots on the workpiece so, it can found in all the Workshops and Industries.
- They are mainly found in Gear Manufacturing.
- The Drum Miller is used to mill the Automobile Cylinder Heads so, the applications of Drum Type can be found in Automobile Manufacturing Industries.
- Tracer or Tracer Controlled Milling Machine is used to machine the Cams, Contoured Surfaces, etc.
Conclusion:
The Milling Machine is a manufacturing machine tool that can found even in small workshops which involve low-level applications. Due to the several types of millers, the miller’s usage is vast and can be found in high-level applications. The technology is upgrading with lots of researches. Accordingly, the technology of millers is also increasing.
Frequently Asked Questions:
What is the purpose of the Milling Machine?
The Purpose of Milling Machine are
- To produce slots on the workpiece.
- To manufacture the Gears, Cams, Grooves.
- To produce the Automobile Cylinder Heads.
What type of Cutting Tool is used in the Milling Machine?
The Multi-Point Cutting Tool is a cutting tool or milling cutter used in Milling Machine.
What is CNC Milling Machine?
CNC Milling Machine is a computer numerical control type, where the pre-defined coding will be uploaded to generate the required workpiece. Thus, the process does not involve much human effort, and most of the work is performed by Computer or Automation itself.
What is Arbor in Milling Machine?
The Arbor is one of the Milling Machine parts or components that is used to fix the Cutting Tool or Milling Cutter.
What is Multi-Point Cutting Tool?
A Multi-Point Cutting Tool is a type of cutting tool that consists of two or more cutting edges or points called Multi-Point. These cutting tools are used in Milling Machines for slotting and grooving purposes. It can be called a Milling Cutte