What is Spot Welding?
Spot Welding can be called Resistance Spot Welding; it is a type of resistance welding that is used to join the thin sheet metals. Unlike arc welding, It does not use any arc, metal electrode, and electrode holder for its working; instead, it will purely work on the pressure and the electricity.
As the name indicates, the resistance spot weld will be used to join the sheet metals in the small spots (or welds). The applications of spot weld are large and significant in heavy productions.
It is necessary to read about the resistance type of welding along with spot weld. So, read about the resistance type of welding here.
Parts Of Spot Welding:
The resistance spot weld works using electricity so, it does consists of electrical parts along with mechanical parts. The parts of spot weld are as follows.
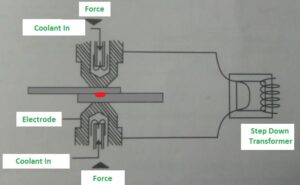
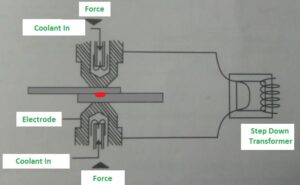
- Copper Electrodes: The copper electrodes are used to weld the sheet metals, they act as current flow conductors.
- Step-down transformer: The step-down transformer helps the resistance spot weld machine supply the power.
- Manual pedal: The pressure is required to apply on the sheet metals for this welding so, the manual pedal will be connected with some mechanism to the electrodes.
- Coolant: The coolant like water is used to cool down the heated electrodes after the welding operation.
Working Process Of Spot Welding:


Step 1: As the resistivity of the copper is less and conduction is more, the copper electrodes are chosen to weld the workpiece. The current is allowed to flow through the two copper electrodes and the workpiece is placed between them.
Step 2: The pedal is used to push the two electrodes to contact whereas; the workpiece is in between both the electrodes, the force is applied on the workpiece by electrodes.
Step 3: The pressure that applied and the current that flowing through the conductors will weaken the spot and joins the two workpieces.
Once the operation is completed, the resistance spot weld electrodes will be cool down with coolant like water.
Materials used for Resistance Spot Welding:
As the process depends upon the resistance of the current so, the resistance spot welding is limited to few metals only. They are as follows.


- Steel or stainless steel and it’s few types
- Aluminum
- Zinc
We can weld the alloys of the above metals whereas; it can able to join the dissimilar metals too.
Advantages Of Spot Welding
The advantages of this type of resistance welding are as follows
- The main advantages of spot welding are that it does not require any filler metals and gases for joining the metal pieces.
- It is easy to join the metals using this type of welding process and does not require any high skilled labours or technicians.
- Simple operation and the fast welding process are other advantages of spot welding.
- The power required to operate is less and no life-risking operations are involved.
- Resistance spot weldings can be used for heavy production purposes due to its fast processing.
Disadvantages Of Spot Welding:
The disadvantages of this type of resistance welding are as follows
- The resistance spot weld cannot be used to weld the thick workpieces.
- We cannot use the coolants in other welding processes as we do in the this type of welding.
- The weld will be broken or fail if the permissible pressure on the workpiece is not achieved.
- If the pressure or current is overflown then the weld spot will appear black and ugly.
Applications Of Spot Welding
The applications of spot weld are
- The resistance spot welding is used to joining the thin sheet metals so, the applications of this type of welding are major in the boiler, tanks manufacturing fields.
- The applications of this type of welding can be observed at Automotive Industries.
- Resistance Spot Welding is used in Aerospace Industries too.
- We can even find the applications of spot weld process in the field of Orthodontics (the field of dentistry or the study of teeth).
Conclusion:
The sheet metals are thin and do not possess any strength as cast iron and steel do so, arc and gas welding will not suitable for the welding of sheet metals. In this scenario, spot weld came into the field and showing its significance.
The resistance spot weld is a permanent joining process and does not require any special electrodes or filler metals to join the workpieces, this is actually what made the resistance spot welding unique from others. We cannot compare spot weld with other types of welding (like arc welding, gas welding) because each type has its significance and role play in its own way.
I appreciated it when you shared that it is easy for metals to join together using this type of welding process and the necessary components. It is crucial for manufacturers to ensure that the right electrodes are used for the operation. I would like to think if a company is doing a spot welding process, it should consider getting the right electrodes for the application from a reliable supplier.